Waterproofing Expansion Joints: Durability and Value of Sika Emseal Products
SUMMARY:
Waterproofing building expansion joints is in many ways dependent on the selection of the right system for the application at hand. Where properly selected, sized, and installed, Sika Emseal has products that perform well beyond their warranty. Ultimate longevity will be situational and depend on many factors such as exposure, geographical climate, amount of cyclical movement, exposure to extraordinary movements, performance of adjacent building materials, maintenance, etc.
In the horizontal plane where properly selected, sized, installed and maintained, Sika Emseal has silicone-coated, pre-compressed, hybrid sealant products that are still performing after 10 or more years. In the horizontal plane, durability is far more affected by situational conditions than vertical-plane applications. Exposure, amount of cycling, traffic, point-loading, abrasion, snow removal, salting, performance of adjacent building materials, and whether or not regular maintenance takes place are among factors that impact durability in any given situation.
Horizontal-plane (ex. parking garage) expansion joints must be, and generally are, considered in the industry to be replacement items. While it is perhaps reasonable to design bridges or parking structures with the intention of thirty or more years of design-life, it is not reasonable to extend these expectations to the expansion joint seals.
A good analogy is the tires on a vehicle. Responsible for handling the full variety and intensity of dynamic loads, abrasion, temperatures, and surface-conditions, tires (like expansion joints) can last with a great degree of variability depending on conditions of operation and maintenance.
By virtue of performing the role of maintaining watertightness under traffic conditions while handling the dynamic movement of structural components, the material selected to seal expansion joint openings will have a substantial impact on the achievability of the design-life goal for any structure. The expansion joint material must, consequently, be properly selected, sized, installed, maintained, repaired or replaced as necessary to ensure proper function.
The ultimate determination of longevity is equally affected by the design, selection, sizing, installation and maintenance of the products as well as by the operating conditions in each project specific situation.
THE FULL EXPLANATION:
Sika Emseal provides up to five-year, limited, project-specific materials warranties on its products. Where a project-specific warranty is not requested, a default one-year, limited, materials warranty applies.
We do not, however, sell our products based on simple durability or warranty statements. Our extensive track record, and the feedback of customers, provides significant evidence of performance success and lowest total cost of ownership expansion joint sealing. In addition to this track record, we sell our products on the basis of performance principles and on the professional ability of those who specify our products to understand these differentiators. Engineers and architects are by nature skeptical and by experience cynical–understandably so. They have been made empty promises of performance for years and are wary of salespeople who lead with unsubstantiated and grandiose claims.
Sika Emseal building expansion joint products work and last because of a combination of:
- product composition
- the physical basis on which they function
- the process by which they are selected and specified
- the manner in which they are delivered to the market
- the manner in which they are installed
- the manner in which they are maintained
In the cases where our products are lasting the longest, this is a consequence of the shared responsibility of the designer or specifier, the contractors involved, ourselves as the material supplier, and the owner of the structure into which they are installed.
Product Composition
Sika Emseal, like all manufacturers has choices when it comes to raw materials. In our foam sealants, for example, we can choose to use lighter, cheaper, mass-produced foam intended for the furniture and bedding market or we can choose to have a custom foam made that meets a specification that better contributes to function and durability. We choose the latter.
In our choice of silicones for the bellows on our products, we have a choice between cheaper silicones containing fillers, or non-filled, higher performing silicones. We choose the latter.
Where the choice exists, based on material size, to manufacture our products from monolithic blocks of foam or, to control the evenness of impregnation dispersion through the use of compression, or vertically compression-bonded laminations, we make that choice situationally to optimize performance.
In our choice of aggregate loading for our Emcrete elastomeric nosing material, we can choose to extend the yield and lower the cost of the material with large-mesh aggregates at high aggregate-to-resin ratios; or we can choose to use more expensive, fine mesh, aggregates at low aggregate-to-resin ratios to preserve flexibility and extend durability. We choose the latter.
You get the idea.
Principles of Expansion Joint Seal Product Performance
Sika Emseal’s products, wherever possible, have been conceived, designed or refined to reduce or eliminate the forces or factors that cause other technologies to fail in the same applications.
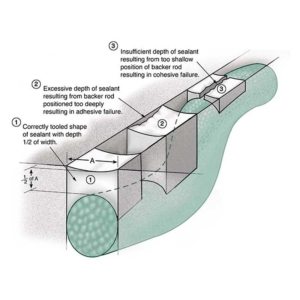
Proper sizing and position of the backer rod that shapes a field tooled sealant can profoundly affect performance.
Where liquid sealant and backer rod fail during joint movement due to tensile stresses at the bond line or within the cured sealant elastomer, Sika Emseal’s pre-compressed, hybrid sealants don’t fail because neither the bond line, nor the bellows are ever in tension. This is true of our vertical plane and horizontal plane and bridge systems.
Where closed-cell EVA-based foam systems fail due to compression set during compression followed by tension during joint opening, Sika Emseal’s precompressed hybrid sealants don’t because of the low-compression-set characteristic of the custom foam we use and because we build each product item for a given joint size from more material than the expected maximum joint opening. This is true of our vertical plane and horizontal plane systems.
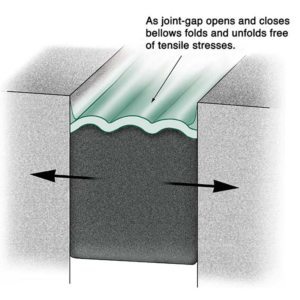
Sika Emseal pioneered a “tensionless” hybrid of precompressed foam and a factory applied and cured silicone bellows. The bond line and bellows are never in tension thereby removing the primary cause of failure for other systems.
In the cases where polyurethane liquid sealants and backer rod suffer due to tensile stresses exacerbated by their susceptibility to durometer fluctuations caused by temperature extremes both hot and cold, as well as by long-term UV exposure, Sika Emseal’s pre-compressed hybrid sealants use high-quality silicone except in special cases such as where pick resistance is the primary specification driver or in situations where a paintable silyl-terminated polyether (STPE) hybrid liquid sealant is a better choice.
In the case of waterproofing roof expansion joints, Sika Emseal’s RoofJoint works where others don’t because the dual-level, roof membrane flanges ensure integration redundancy and the double-cell sealing gland ensures sealing redundancy in the event of puncturing or damage to the exposed upper cell wall. Furthermore, the RoofJoint, when used with our RoofJoint Closures, addresses the intersection of the roof and corresponding wall expansion joints through the availability of factory-fabricated transitions.
Our Seismic Joint System works where “self-centering bar, gutter and cover plate systems” fail because SJS is watertight at the deck surface, secures to the concrete without invasive anchors, employs no hard connections to the concrete, because the cover-plate is not anchored to the concrete, and because continuity of seal is assured.
Expansion Joint Selection and Design
Waterproofing expansion joints and the durability of any product is as affected by the designer as the manufacturer.
While many manufacturers defer and react to designs and material selections made by architects, engineers and consultants, Sika Emseal, where invited into the process, engages collaboratively to facilitate consideration by the designer of numerous design issues that affect joint sealing and durability.
Design issues that affect joint sealing may include by are not limited to:
- continuity of seal
- substrate configuration
- joint movement expectations
- traffic and loading expectations
- joint sizing in relationship to temperature, product movement capability, and time of joint forming and installation
- properly designed, specified, manufactured and installed transitions and terminations
- relationship to adjacent waterproofing and other building components
- acoustic requirements
- fire, hurricane, tornado and other performance expectations; etc.
To facilitate collaboration, Sika Emseal invests in many ways that other manufacturers, for cost reasons, don’t. These include:
- regionalized sales managers paired to inside techs to ensure availability of a principle point of contact
- the development of systems for communication of expansion joint layout in three dimensions
- the development of tools for calculation and discussion of joint movements
- the use of web conferencing for enhanced collaboration
- the development and maintenance of a content rich website with an open-source sharing of of CAD, BIM and 3-D expansion joint details and other content to facilitate specification
- the use of finite element analysis (FEA) modeling
- the use of third-party engineers for engineered judgments
- The offering of in-depth, AIA registered and SWRI-Validated training for all stakeholders
Expansion Joint Installation
The durability of any product is additionally affected as much by contractors as it is the manufacturer and designer.
The General Contractor’s role in ensuring expansion joint durability extends to the coordination of all trades whose actions affect the proper location and construction of unobstructed, properly sized, properly aligned expansion joint opening.
The subcontractor responsible for the installation of the expansion joint must ensure that the material purchased is properly sized for the field conditions present and must execute installation in compliance with the manufacturer’s standard procedures, their own standards of professional care and stewardship, industry standards of best practice, as well as by bringing project-specific, situational judgment and care to the conditions at hand.
Pre-Sale Quality Assurance
Perhaps the most significant differentiator of Sika Emseal’s in regard to installation quality is its Checklist-based ordering process. Most manufacturers are content to ship
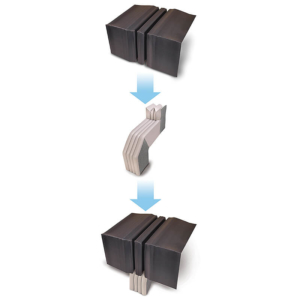
The transition from roof expansion joint to wall expansion joint has been a long overlooked condition. Making this plane change has historically been left to cobbling together the roof system and the wall expansion joint with caulk and flashing. RoofJoint from Emseal is married to Seismic Colorseal through a factory-fabricated Roof Joint closure. The underside of the RoofJoint extrusion matches the profile of the closure. The interface is sealed with silicone provided. The factory welded, reinforced, and leak tested downturn in the RoofJoint can be factory welded to long lengths of straight run material, minimizing field welds.
straight runs of what is ordered and shift responsibility for selection to the purchaser. By contrast, Sika Emseal endeavors whenever the information is provided, to ship what is needed based on the contractor’s gathering of verified field conditions. This information wherever possible considers and provides for changes in plane and direction in the run of the joint and for proper termination or transition to other joint systems at the end of each joint run.
This process of vetting orders before shipment usually represents a change in culture for contractors. However, when embraced, it results in the reduction of instances of the wrong material or size being used, and reduces material mis-orders, returns, failures and callbacks. Managing this process requires a commitment by Sika Emseal of resources, and internal training and culture development to embrace this non-traditional approach to building material supply.
Continuing Education
To further assist the contracting community in this regard, in addition to the production of detailed installation guides and videos, Sika Emseal invests in making available in-house, SWRI-Validated training, project-specific training, and custom in-firm or webinar training for contractors, architects, owners, engineers and our reps and distributors. Sika Emseal also has invested in and makes available web-based, video, online chat, and webinar technology to guide installers through installations or site issues in real time.
Building Expansion Joint Maintenance
Sika Emseal products are inherently tough and generally forgiving of neglect. Their ultimate durability, however, depending on the application, can be significantly affected by the actions of the owner or manager of the structure into which they are installed.
Unless vandalized, installations of our pre-compressed hybrid sealants in vertical-plane (wall) applications require little if any maintenance. Durability in applications in the horizontal plane, depending on the operating environment, can be significantly prolonged by good maintenance.
In non-traffic applications, maintenance can be minimal but occasional (at the owner’s discretion and judgment of frequency) removal of dirt and debris from the joint surface and inspection and repair or replacement of any damage will contribute to longer life.
In highly trafficked applications, regular maintenance will significantly enhance service life and allows for the addressing of small problems before they become big. At intervals, suited to the operating conditions but at least annually, cleaning, inspection, repair of minor damage or replacement of severely damaged sections of material will dramatically prolong the functional product lifespan.
On the other hand, improper maintenance, such as the use of aggressive, mechanized brooms or scrubbers, extreme pressure washing, and the failure to use rubber-tipped snow-plow blades will all negatively affect product durability. Care must be taken to use appropriate maintenance methods and equipment.
Partnerships
Sika Emseal partners with independent manufacturer’s representatives, distributors and agents worldwide. While independently owned entities, the behavior of these partners can dramatically affect not only the durability of materials but also the expectations of customers, specifiers and owners.
Sika Emseal’s expectations are that these partners bring their own professional propriety to the relationship as well as adopt Sika Emseal’s principles and practices in ensuring that all parties involved in the delivery of lasting expansion joint solutions own their share of this responsibility.
The Bottom Line:
Sika Emseal has worked diligently through R&D and innovation to remove wherever possible from the basis of performance of our products, the forces and factors that cause liquid-sealant and backer rod and other common or predecessor joint sealing technologies to fail. As a result, it is reasonable to expect expansion joints waterproofed with Sika Emseal products to perform better and longer than alternatives.
The ultimate determination of longevity is equally affected by the design, selection, sizing, installation and maintenance of the products as well as by the operating conditions in each project specific situation.